Operational efficiency is a crucial aspect of any successful business. It refers to the ability of a company to maximize productivity while minimizing costs and waste. Achieving operational efficiency requires a deep understanding of the various processes that make up a business and the role of technology in optimizing those processes.
Measuring operational efficiency is a key step in identifying areas that need improvement. There are several metrics that businesses can use to measure their operational efficiency, including productivity, quality, and customer satisfaction.
By tracking these metrics and analyzing the data, businesses can identify areas where they fall short and develop strategies to improve efficiency.
Key Takeaways
- Operational efficiency is essential for business success.
- Measuring operational efficiency is crucial to identify areas for improvement.
- Metrics such as productivity, quality, and customer satisfaction can be used to measure operational efficiency.
Understanding Operational Efficiency
Operational efficiency is an organization’s ability to utilize its resources effectively to achieve its objectives. It measures how well an organization performs in terms of its processes, productivity, and performance. By measuring operational efficiency, organizations can identify the areas where they need to improve and make necessary changes to achieve better results.
Time
Time is a critical factor in measuring operational efficiency. Measuring the time taken to complete processes and tasks is critical. By doing so, organizations can identify areas where they are wasting time and resources and take corrective actions to improve their efficiency.
Productivity
Productivity is another essential factor to consider when measuring operational efficiency. It is the measure of the output produced per unit of input. Organizations can identify areas where they need to improve their processes and increase their output by measuring productivity.
Efficiency
Efficiency is the ratio of the output to the input. It is essential to measure efficiency to identify areas where an organization is wasting resources and take corrective actions to improve its efficiency.
Measuring operational efficiency involves measuring the processes used by the organization. In doing so, organizations can identify areas where they need to improve their processes and make necessary changes to achieve better results.
Performance
Performance is another critical factor to consider when measuring operational efficiency. It is the measure of how well an organization is performing in terms of its objectives. By measuring performance, organizations can identify areas where they need to improve and take corrective actions to achieve better results.
Continuous improvement is essential to maintain operational efficiency. Organizations need to continuously monitor their processes and identify areas where they need to improve. By doing so, they can make necessary changes to achieve better results and maintain their operational efficiency.
The Role of Technology in Operational Efficiency
Technology plays a key role in measuring operational efficiency. With the help of software and data, businesses can identify areas that need improvement and make informed decisions. Automation can streamline processes, reduce errors, and improve productivity, leading to cost savings and increased profitability.
Technology also enables businesses to track and analyze data in real time, allowing them to make quick adjustments to improve operations. Dashboards visually represent key performance indicators, making monitoring progress easier and identifying areas that need attention.
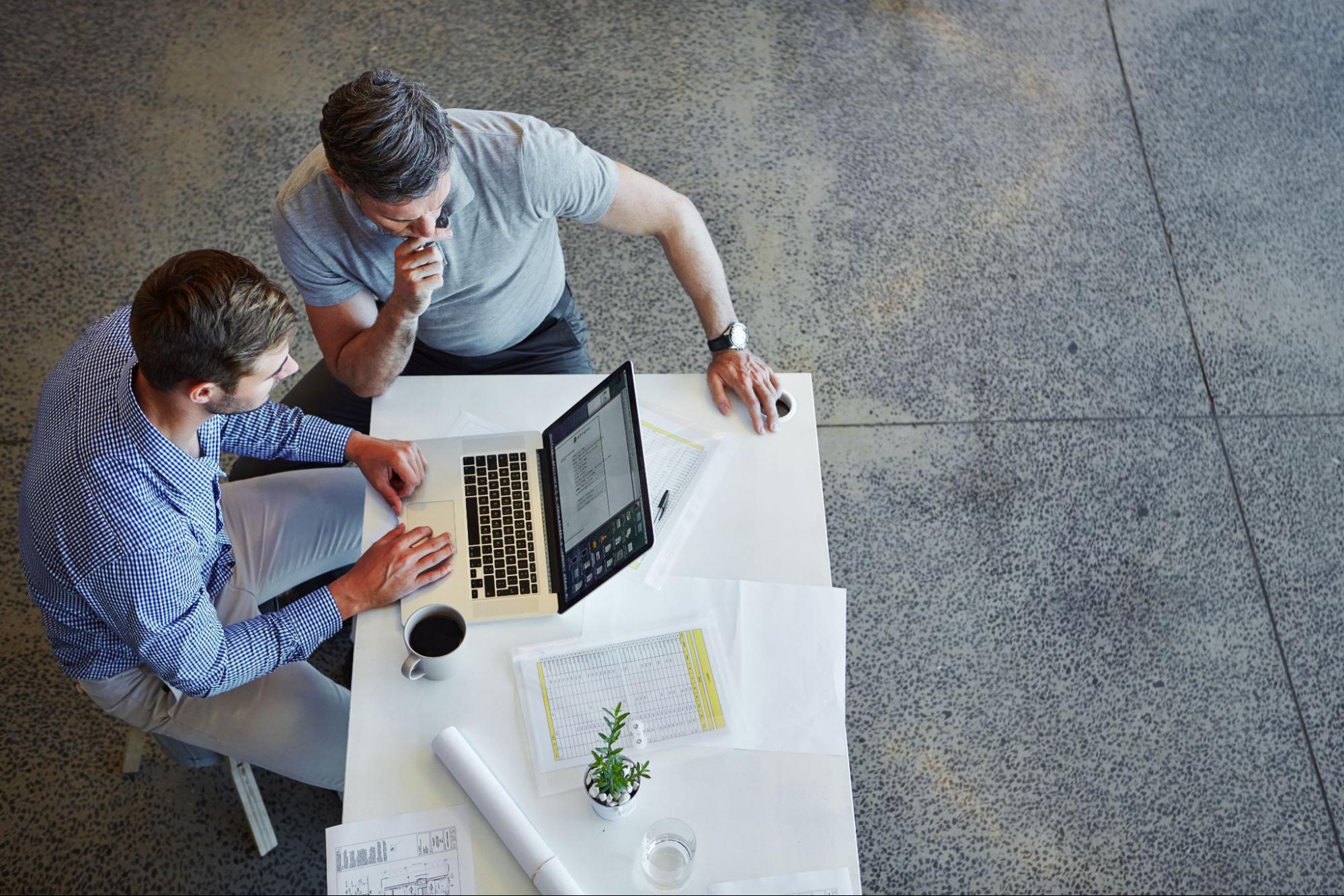
Systems such as enterprise resource planning (ERP) and customer relationship management (CRM) can integrate data from various departments and provide a comprehensive view of operations. This enables businesses to make informed decisions and improve overall efficiency.
The Impact of Operational Efficiency on Business Financials
Operational efficiency has a significant impact on a business’s financials. By optimizing operations, a company can reduce costs and increase profitability. It allows businesses to produce more goods or services with fewer resources, reducing operating expenses and the cost of goods sold.
A company’s financial health is directly linked to its capacity to manage costs. When a business operates efficiently, it can manage its costs better, reducing the amount of money it spends on salaries, wages, and other expenses. This, in turn, can lead to increased revenue and profitability.
Efficient operations also help businesses manage their debt and operating costs. By reducing the amount of money spent on operating expenses, a company can free up cash flow, which can be used to pay off debt or invest in growth opportunities.
Cost management is an integral aspect of operational efficiency. Businesses that can effectively manage their costs can improve their profitability and financial health. A company can improve its bottom line and increase its cash flow by identifying areas where costs can be reduced.
Businesses can reduce costs, increase profitability, and improve their financial health by optimizing operations. Companies that prioritize operational efficiency and cost management are more likely to succeed in the long run.
Operational Efficiency in Production and Sales
Operational efficiency is critical in production and sales to ensure the company meets its targets and delivers value to customers. To measure operational efficiency, it is necessary to track the following entities: products, sales, output, growth, customer satisfaction, quality, services, value, production, input, equipment, inventory, direct labor costs, and direct material costs.
One way to measure operational efficiency in production and sales is to track the output per employee. This metric helps identify the workforce’s productivity and can help identify areas for improvement. Additionally, tracking inventory levels can help ensure the company meets customer demand while minimizing waste.
Another way to measure operational efficiency is to track the direct labor costs and direct material costs. This metric helps to identify the cost of production and can help to identify areas where the company can reduce costs and improve profitability. Additionally, tracking customer satisfaction can help ensure that the company delivers value to its customers and help identify improvement areas.
To improve operational efficiency in production and sales, it is essential to invest in equipment and technology that can help to streamline processes and improve productivity—ensuring that the company delivers high-quality products and services that meet customer needs and expectations is also critical.
Operational efficiency is critical in production and sales to ensure the company meets its targets and delivers value to customers. By tracking key metrics and investing in equipment and technology, companies can improve productivity, reduce costs, and improve profitability.
Human Resources and Operational Efficiency

Human resources play a critical role in measuring operational efficiency. It is important to have the right people in the right roles to ensure that the company is running at peak performance. This means hiring employees with the necessary skills and experience and providing them with adequate training and support to perform their jobs effectively.
Employee performance is a key metric for measuring operational efficiency. By setting clear KPIs and regularly monitoring employee performance, companies can identify areas for improvement and take corrective action as necessary. This can help to reduce waste, increase productivity, and improve overall efficiency.
Effective leadership and project management are also critical for maximizing operational efficiency. By creating a positive company culture that values teamwork and collaboration, companies can foster a sense of ownership and accountability among team members. This can lead to improved employee morale, higher levels of engagement, and ultimately better results.
Operational Efficiency and Customer Service
A company’s power to provide excellent customer service is a key indicator of its operational efficiency.
Customers are the lifeblood of any business, and their satisfaction is essential for long-term success. A company that can provide excellent customer service is more likely to retain customers, receive positive reviews, and attract new customers through word of mouth.
Companies can use metrics such as response time, resolution time, and customer satisfaction scores to measure operational efficiency in customer service. By tracking these metrics, companies can identify areas for improvement and make data-driven decisions to improve their customer service operations.
Besides metrics, companies can also invest in training their customer service representatives to provide excellent service. This can include teaching them how to handle difficult customers, communicate effectively, and resolve issues quickly and efficiently.
Overall, operational efficiency and customer service go hand in hand. Companies can increase customer satisfaction, retention, and their bottom line by measuring and improving customer service operations.
Measuring Operational Efficiency
Measuring operational efficiency is important for businesses to evaluate their performance and identify areas for improvement. Key performance indicators (KPIs) and operational efficiency ratios are commonly used to measure operational efficiency.
Key performance indicators (KPIs)
KPIs are specific metrics that help businesses track progress toward their goals. Some common KPIs used to measure operational efficiency include inventory turnover, customer satisfaction, and employee productivity.
Operational Efficiency
Operational efficiency ratios are financial metrics that measure how well a business is using its resources to generate revenue. The asset and inventory turnover ratios are the most commonly used operational efficiency ratios.
Key Metrics
To measure operational efficiency, businesses should also consider using key metrics such as revenue growth, profit margin, and return on investment. These metrics provide a comprehensive view of a business’s financial performance and can help identify areas for improvement.
Overall, measuring operational efficiency is essential for businesses to stay competitive and achieve long-term success. By using a combination of KPIs, operational efficiency ratios, and key metrics, businesses can track their progress and make data-driven decisions to improve their operations.
Strategies to Improve Operational Efficiency
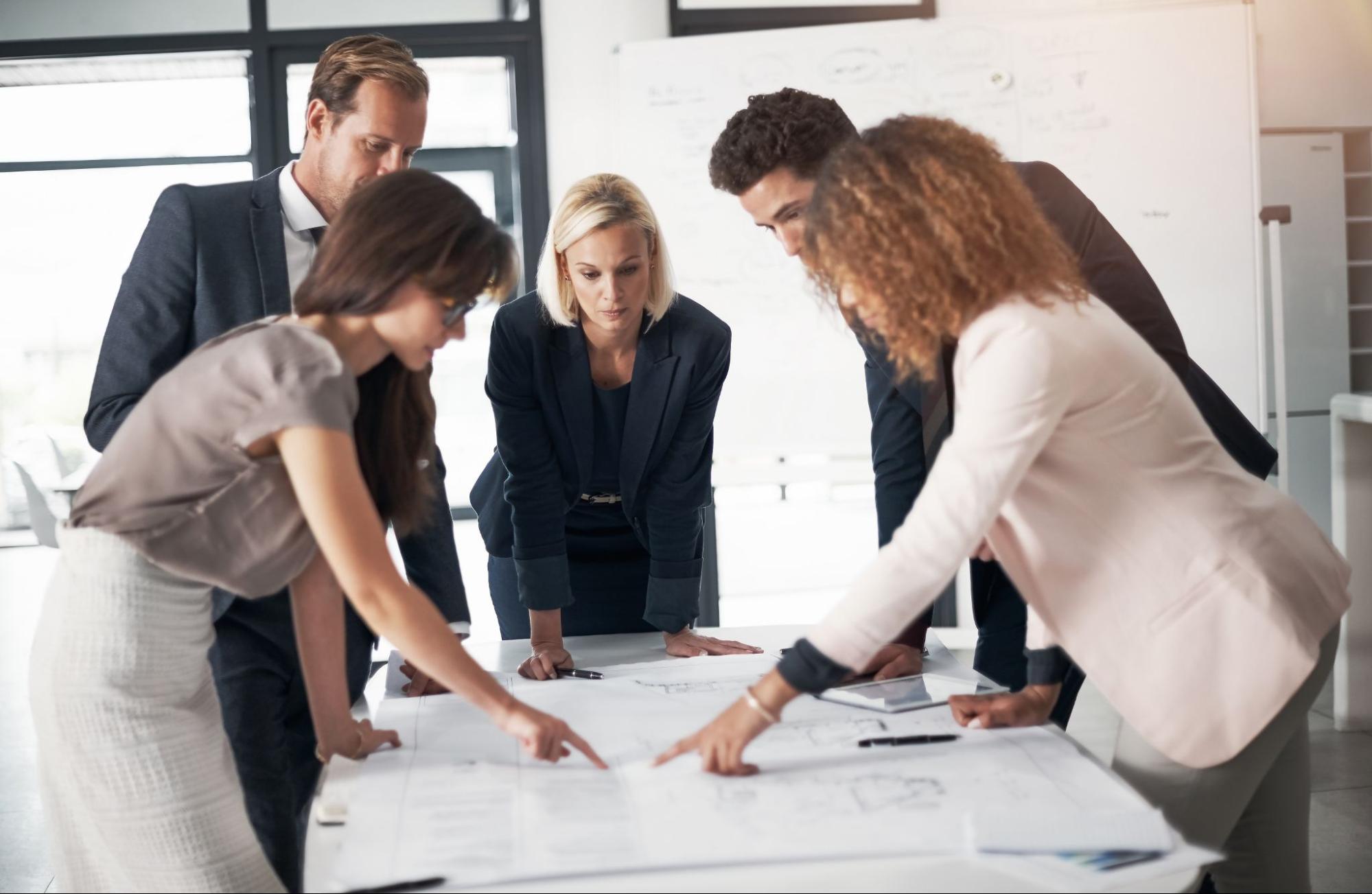
Improving operational efficiency requires a strategic approach that addresses bottlenecks in workflows. One of the best practices to improve operational efficiency is to identify the root cause of the bottleneck and then develop a strategy to address it. This could involve reorganizing workflows, automating processes, or investing in new technology.
Another strategy to improve operational efficiency is to optimize workflows to reduce waste and increase productivity. This could involve streamlining processes, eliminating unnecessary steps, or standardizing procedures. By optimizing workflows, you can improve efficiency and reduce costs while also ensuring that your team is working at peak performance.
One of the most effective ways to improve operational efficiency is to invest in employee training and development. By providing your team with the skills and knowledge they need to succeed, you can empower them to take on new challenges and responsibilities, which can lead to increased productivity and efficiency.
It’s crucial to regularly review and evaluate your operational processes to identify areas for improvement. You can track progress and identify opportunities to optimize workflows and improve efficiency by monitoring key performance indicators and metrics.
Overall, improving operational efficiency requires a combination of strategy, best practices, and a commitment to continuous improvement. Adopting a proactive approach and investing in the right tools and resources can streamline workflows, reduce costs, and increase productivity.
Operational Efficiency in the Market and Industry
Operational efficiency is critical for businesses to stay competitive in the market. A company’s operational efficiency can be a significant factor that sets it apart from its competitors. In today’s fast-paced business world, companies need to be efficient and effective to stay ahead of the competition.
Industry and market trends can significantly affect the operational efficiency of a business. Companies need to keep track of trends and changes in the market and industry to stay competitive and profitable. By keeping up with the latest trends and adopting new technologies, companies can improve their operational efficiency and stay ahead of the curve.
Marketing is also an indispensable aspect of operational efficiency. Effective marketing strategies can help businesses reach their target audience and increase their customer base. Companies can tailor their marketing strategies to improve operational efficiency and business growth by understanding customers’ needs and preferences.
Competition is another critical factor that can affect a company’s operational efficiency. By keeping an eye on their competitors’ strategies, companies can identify areas where they need to improve and stay ahead of the competition. Companies can improve their operational efficiency and profitability by adopting best practices and learning from their competitors.
Companies can improve their operational efficiency and stay ahead of the curve by keeping up with the latest trends, adopting new technologies, and learning from their competitors.
Operational Efficiency from the Perspective of Stakeholders
Operational efficiency is paramount to any successful business, and stakeholders play a significant role in measuring it. Investors, operations managers, executives, and successful businesses all have different priorities when it comes to operational efficiency.
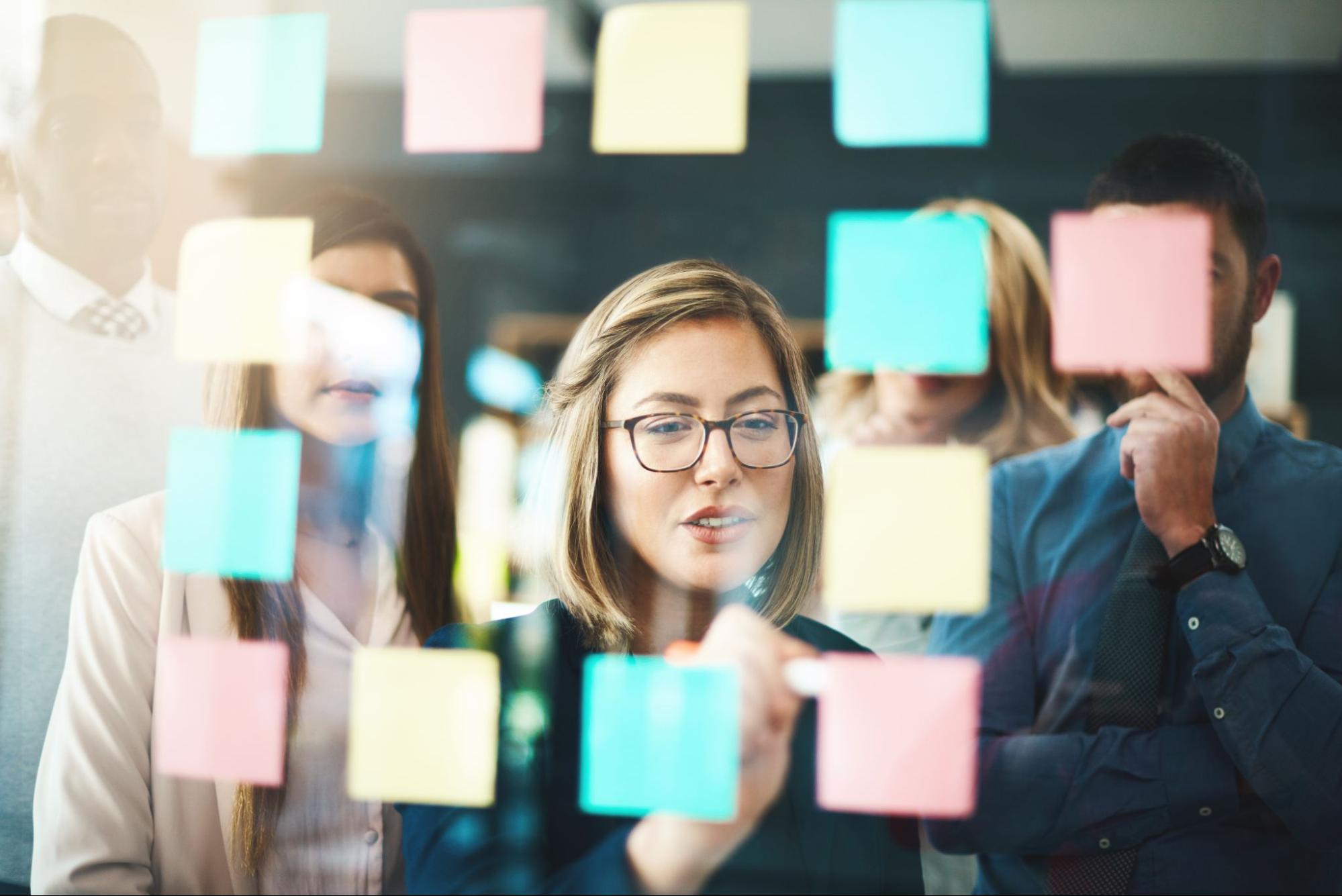
- Investors are interested in a company’s financial returns, and operational efficiency is a critical factor in determining those returns. They look at metrics such as return on investment (ROI) and profit margins to assess the company’s operational efficiency.
- Operations managers focus on the business’s day-to-day operations and are concerned with optimizing processes and reducing waste. They use metrics such as cycle time, productivity, and defect rates to measure operational efficiency.
- Executives are responsible for the overall strategy and direction of the company. They look at operational efficiency from a high-level perspective and use revenue growth and market share metrics to assess the company’s performance.
- Successful businesses understand that operational efficiency is essential for long-term success. They prioritize continuous improvement and invest in technologies and processes that improve efficiency and reduce costs.
Stakeholders have different priorities when it comes to measuring operational efficiency. Investors focus on financial returns, operations managers optimize processes, executives assess the company’s performance, and successful businesses prioritize continuous improvement.
Conclusion
Measuring operational efficiency is crucial for businesses to reflect on their current performance and make better decisions for the future. By presenting data in an organized and understandable way, businesses can quickly identify areas that need improvement and adjust accordingly.
One way to measure operational efficiency is through scheduling. By creating a schedule that maximizes productivity and minimizes downtime, businesses can ensure that they are using their resources effectively. This can lead to higher returns and more efficient payroll management.
Another important factor in measuring operational efficiency is decision-making. Businesses can avoid costly mistakes and streamline their operations by analyzing data and making informed decisions. This can lead to increased profitability and a more successful business overall.
Frequently Asked Questions
Q. What are some operational efficiency metrics to track?
Key performance indicators (KPIs) are critical metrics to track operational efficiency. Some essential KPIs include cycle time, lead time, throughput, and capacity utilization. Tracking these metrics helps to identify bottlenecks and inefficiencies in the production process.
Q. What strategies can be used to improve operational efficiency?
Organizations can implement several strategies to improve operational efficiency, such as automation, process optimization, and employee training. Automation can help reduce manual labor and errors and increase productivity.
Process optimization involves analyzing the production process to identify bottlenecks and inefficiencies and implementing solutions to improve overall efficiency. Employee training can help to improve skills and knowledge, leading to better performance and increased efficiency.
Q. What is a good operating efficiency ratio to aim for?
A good operating efficiency ratio varies by industry, but generally, a ratio of 80% or higher is considered good. This means that 80% or more of the available resources are being used effectively to produce goods or services.
Q. How can operational effectiveness be assessed?
Operational effectiveness can be assessed by measuring KPIs, analyzing data, and conducting audits. Regularly measuring KPIs helps to identify areas for improvement, and data analysis can help to identify trends and patterns in production. Conducting audits ensures that processes are being followed correctly and identifies areas where improvements can be made.
Q. What are some examples of operational efficiency in practice?
Operational efficiency can be seen in various industries, such as manufacturing, healthcare, and retail. For example, a manufacturing company may implement automation to reduce manual labor and increase productivity.
A healthcare organization may optimize the patient intake process to reduce wait times and improve patient satisfaction. A retail store may implement inventory management systems to reduce waste and improve profitability.
Q. How can production efficiency be measured effectively?
Production efficiency can be measured by tracking cycle time, throughput, and capacity utilization KPIs. Additionally, conducting time studies and analyzing data can help to identify areas where improvements can be made. Regularly reviewing and analyzing production data helps ensure the production process runs efficiently and effectively.